Acoustic Monitoring
Acoustic signals can carry information about the structural integrity of objects and machines. Such acoustic signals could stem from passively “listening” to the device, for example to rotating machinery, or from being actively evoked. For more than a century, train wheels are being assessed for cracks by hamming on the wheel rim and listening to the sound. Similarly, when purchasing pottery or glasses, you might also hit the rim to listen for cracks.
In the light of climate change, green energy production is important. Reliable monitoring of wind turbines or geothermal pumps is essential for their efficient and secure operation. Our research focusses on predicting material properties and operating conditions of wind turbines and geothermal pumps by analyzing features related to their sound quality.
Key findings
- Perceptual features used by human examiners when judging the health of wind-turbine rotor-blades (Andreisek, Große & Seeber, 2015)
- Computerized test for the health of wind-turbine rotor-blades using acoustic feature extraction and machine learning (Andreisek & Seeber, 2018)
- Training tool for the acoustic inspection of wind-turbine rotor-blades (Andreisek et al., 2016)
- Health index of a deep centrifugal pump using unsupervised machine learning of sound quality features (Kolotzek, Baumann & Seeber, GAB-Wissenstransfer 2021)
Perception-inspired testing for structural integrity of wind turbine rotor blades
Wind power plants contribute remarkably towards achieving an independent and green energy supply. In order to guarantee the reliability of those engineering structures over a lifetime of 20 years, they have to be checked on a regular basis.
An established non-destructive testing method for the inspection of wind turbine rotor blades is the (coin-) tap test. A skilled inspector utilizes a mallet to tap the material, thereby eliciting local body-born vibrations that emit audible acoustic signals. These acoustic signals reveal information about the integrity of the material to the trained ear of an experienced inspector.
A tap sound can be described as less impulsive and quieter than another, but does that mean there is a defect present? Sound Quality measures, such as subjective ratings of experienced inspectors in connection with psychoacoustic correlates, can help us understand which acoustic information is important for a robust identification of defects (Andreisek, Große & Seeber, 2015). From models of the auditory system we know how humans process and make use of certain aspects of sounds, which helps us to derive targeted features. Statistical classification techniques then combine these features into a value that expresses the presence and size of the damage (Andreisek & Seeber, 2018).
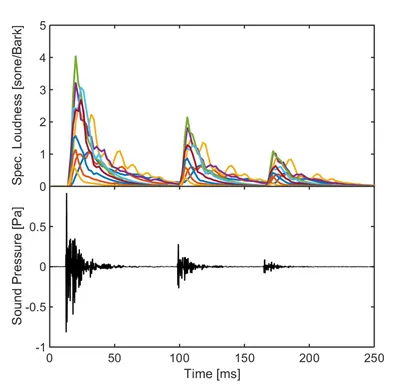
Vibro-acoustic monitoring of a downhole geothermal pump
Using geothermal energy to generate electricity is an emerging alternative. However, the downhole machines, such as the centrifugal pump, are exposed to adverse temperature and pressure conditions that reduce the lifetime of the pump and its effectiveness. An accurate monitoring is essential to organize punctual maintenance to extend both lifetime and efficiency.
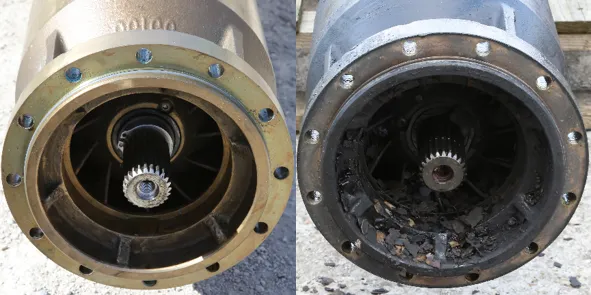
Installing, e.g., vibro-acoustic sensors near the pump is not trivial because of the temperature and pressure conditions downhole. Therefore, installing sensors above ground might be a promising method for monitoring the downhole pump.
By extracting features usually known for sound quality and by using unsupervised, non-linear machine learning algorithms, it is possible to predict a health index of the downhole pump to punctually organize maintenance (Kolotzek, Seeber & Baumann, 2019).
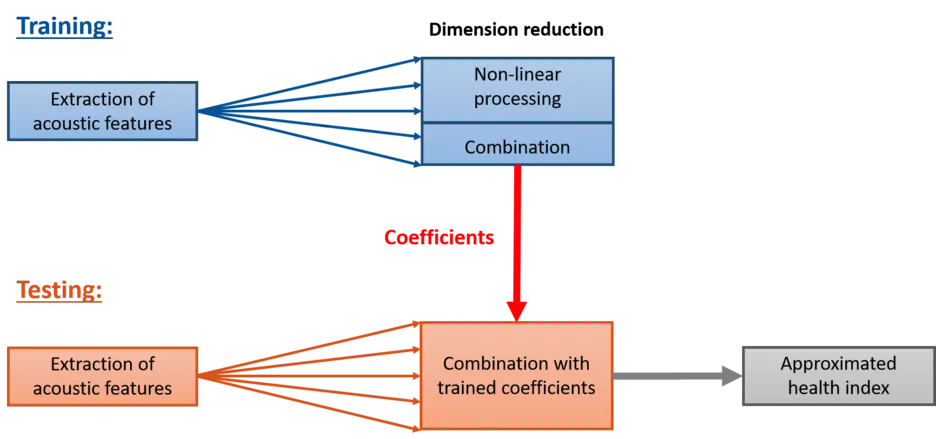
Team members involved in acoustic monitoring
Current:
Norbert F. Bischof, M.Sc.
Past:
Gaetano Andreisek, M.Sc.