Tactile Mechatronic Systems
Inspired by the human sense of touch with its Golgi tendon - an organ for measuring muscle tension in the human musculoskeletal system - or tactile perception in the skin, designing robots with proprioceptive force/torque sensing in their joints and link structure as well as sensory skins at the surface level endows them with the tactile capabilities to sensitively and safely interact with their environment via tactile control. The research we conduct in this area considers the synergistic integration of mechanical engineering, sensory systems, electronics, and control in the design of complex mechatronic systems for tactile robots. This ranges from torque controlled drives and viscoleastic actuators to tactile exoprostheses and hands; together with methods for proprioceptive and tactile sensing, high performance communication and high-fidelity control.
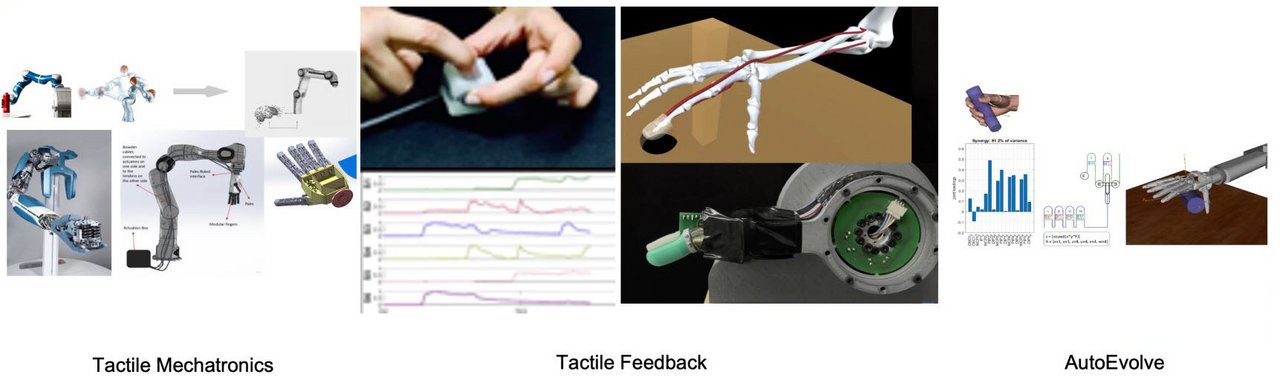
Contributions
Collaborative and Tactile Robots depicts the tactile robot platforms to which development our group contributed to. Our work has lead to the design of state-of-the-art highly integrated torque-controlled and elastic actuators and lightweight robots capable of elegant physical interaction with their surroundings. Early works covered the DLR lightweight robot III (LWR-III) [171, 172], which later formed the basis of the well-known humanoid DLR-systems Justin [173] and Toro [174]. Later, the DLR hand-arm system HASy with with variable stiffness actuators (VSA) in every joint was developed [175]. This mimics the human musculoskeletal system in terms of variable passive joint compliance and the elastic energy storage during highly-dynamic energy-efficient motions and tasks. We proposed novel soft actuator concepts for tactile robots with torque control [176]. Further examples are tendon-driven humanoid wrists [177] or the recently introduced Bi-Stiffness Actuator (BSA)[13]. The latter incorporate clutches and multi-articular actuation for dynamic manipulation. It enables link decoupling to precisely store elastic energy in the joint, giving direct control over energy transfer timing.
The most noted example of our work is the Franka Emika Robot [38], the world’s first commercial and fully safety certified tactile robot. In contrast to classical collaborative robots, the Franka Emika Robot was designed to be fully force-controlled to enable the sensing of even the slightest contact with the environment and react with compliant and safe behavior. This philosophy was further developed into Garmi [178], a humanoid robot conceived to assist the elderly with activities of daily living.
AutoEvolve
To build a systematic framework for the co-evolution of embodiment and intelligence in robotics, our group currently introduces the scientific foundation of a new principle coined the AutoEvolve Cycle. First works focus on the automatic specification, design and AI-empowered construction of robot fingertips [180]. Overall, the AutoEvolve Cycle structures the advancing co-evolution of embodiment and intelligence into five phases leveraging the cooperative intelligence of human and artificial intelligence. They cover i.) the AI-assisted design of the robot, which generates the blueprint of the next robot generation, ii.) the construction of the robot platform, also by making use of AI-based and optimization methods, iii.) the understanding of the self and the world to generate models of the embodiment and the environment, iv.) the establishment of the ability to interact, control, and plan to enable the robot to execute complex policies and v.) the evaluation of the skills of the robot with respect to the defined R-Levels.
[13] Dennis Ossadnik, Mehmet C Yildirim, Fan Wu, Abdalla Swikir, Hugo TM Kussaba, Saeed Abdolshah, and Sami Haddadin. “BSA-Bi-Stiffness Actuation for optimally exploiting intrinsic compliance and inertial coupling effects in elastic joint robots”. In: 2022 IEEE/RSJ International Conference on Intelligent Robots and Systems (IROS). IEEE. 2022, pp. 3536–3543.
[38] Sami Haddadin, Sven Parusel, Lars Johannsmeier, Saskia Golz, Simon Gabl, Florian Walch, Mohamadreza Sabaghian, Christoph Jähne, Lukas Hausperger, and Simon Haddadin. “The Franka Emika Robot: A Reference Platform for Robotics Research and Education”. In: IEEE Robotics & Automation Magazine 29.2 (2022), pp. 46–64.
[171] Alin Albu-Schäffer, Sami Haddadin, Ch Ott, Andreas Stemmer, Thomas Wimböck, and Gerhard Hirzinger. “The DLR lightweight robot: design and control concepts for robots in human environments”. In: Industrial Robot: an international journal (2007).
[172] Robert Burger, Sami Haddadin, Georg Plank, Sven Parusel, and Gerhard Hirzinger. “The driver concept for the DLR Lightweight Robot III”. In: IEEE/RSJ International Conference on Intelligent Robots and Systems (IROS). 2010, pp. 5453–5459.
[173] Ch. Ott, O. Eiberger, W. Friedl, B. Bauml, U. Hillenbrand, Ch. Borst, A. Albu-Schaffer, B. Brunner, H. Hirschmuller, S. Kielhofer, R. Konietschke, M. Suppa, T. Wimbock, F. Zacharias, and G. Hirzinger. “A Humanoid Two-Arm System for Dexterous Manipulation”. In: 2006 6th IEEE-RAS International Conference on Humanoid Robots. 2006, pp. 276–283.
[174] Johannes Englsberger, Alexander Werner, Christian Ott, Bernd Henze, Maximo A. Roa, Gianluca Garofalo, Robert Burger, Alexander Beyer, Oliver Eiberger, Korbinian Schmid, and Alin Albu-Schäffer. “Overview of the torque-controlled humanoid robot TORO”. In: 2014 IEEE-RAS International Conference on Humanoid Robots. 2014, pp. 916–923.
[175] Markus Grebenstein, Alin Albu-Schäffer, Thomas Bahls, Maxime Chalon, Oliver Eiberger, Werner Friedl, Robin Gruber, Sami Haddadin, Ulrich Hagn, Robert Haslinger, Hannes Höppner, Stefan Jörg, Mathias Nickl, Alexander Nothhelfer, Florian Petit, Josef Reill, Nikolaus Seitz, Thomas Wimböck, Sebastian Wolf, Tilo Wüsthoff, and Gerd Hirzinger. “The DLR hand arm system”. In: 2011 IEEE International Conference on Robotics and Automation. 2011, pp. 3175–3182.
[176] Oliver Eiberger, Sami Haddadin, Michael Weis, Alin Albu-Schäffer, and Gerd Hirzinger. “On joint design with intrinsic variable compliance: derivation of the DLR QA-Joint.” In: Robotics and Automation (ICRA), 2010 IEEE International Conference on. 2010, pp. 1687–1694.
[177] Alexander Toedtheide, Johannes Kühn, Edmundo Pozo Fortunic, and Sami Haddadin. “An Integrated, Force-Sensitive, Impedance Controlled, Tendon-Driven Wrist: Design, Modeling, and Control”. In: 2020 IEEE-RAS 20th International Conference on Humanoid Robots (Humanoids). IEEE. 2021, pp. 25–32.
[178] Mario Tröbinger, Christoph Jähne, Zheng Qu, Jean Elsner, Anton Reindl, Sebastian Getz, Thore Goll, Benjamin Loinger, Tamara Loibl, Christoph Kugler, et al. “Introducing GARMI-a service robotics platform to support the elderly at home: design philosophy, system overview and first results”. In: IEEE Robotics and Automation Letters (RA-L) 6.3 (2021), pp. 5857–5864.
[180] Johannes Ringwald, Samuel Schneider, Lingyun Chen, Dennis Knobbe, Lars Johannsmeier, Abdalla Swikir, and Sami Haddadin. “Towards Task-Specific Modular Gripper Fingers: Automatic Production of Fingertip Mechanics”. In: IEEE Robotics and Automation Letters 8.3 (2023), pp. 1866–1873.